3D printing can be used to quickly create product models and prototypes. It also helps reduce redesign cycles and allows the creation of multiple SKUs within a short period of time.
There are many different types of 3D printers. They range from those that can fit on a desk to industrial-sized units that use laser sintering or stereolithography processes. Contact By3Design now!
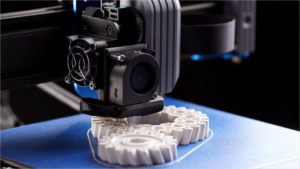
In the fast-paced world of today’s consumer market, product development and launch cycles must be accelerated to stay competitive. This is where rapid prototyping comes in to play a key role. Rapid prototyping enables companies to develop and test a new product much more quickly, reducing the time to market and saving costs by avoiding costly redesigns.
The process begins when a customer provides a drawing exchange format (DXF) file of their fully dimensioned part. This is downloaded into Sur-Seal’s nesting software and a prototype is created within 24-48 hours, if the raw materials are in stock.
A physical model of the part can be made using a variety of methods, including injection molding, CNC machining, vacuum casting, or industrial-grade 3D printing. The goal is to create a functional prototype that looks as close as possible to the final product and allows for physical testing to find any flaws in design or functionality that may be missed during virtual computer simulations.
When the results of physical testing are known, engineers can use the results to revise and optimize the final design for manufacturing. This will enable them to meet quality and performance requirements, while achieving the desired cost structure.
In addition to being able to test the function of a product, rapid prototyping also allows for the consolidation of multiple machined or fabricated parts into one single unit that is produced via an additive technology such as Selective Laser Sintering (SLS), Direct Metal Laser Sintering (DMLS), and HP Multi Jet Fusion (MJF). This can reduce overall assembly and production costs.
To get the most out of the rapid prototyping process, it’s important to set a clear test goal from the start and involve all stakeholders. The results from physical testing can be used to inform design changes and improve usability, making the process more effective. It is also important to choose a material that closely resembles the product’s intended material properties and to account for tolerances so that all parts fit together properly. For example, the wrong choice of plastic can lead to a prototype that doesn’t look or work like the final product.
Manufacturing Aids
Unlike traditional manufacturing methods, which require extensive upfront investment to produce new parts and products, 3D printing can be used to quickly prototype and iterate on design concepts. This makes it easier to gather feedback from customers and investors on a tangible physical prototype. Additionally, when problems are discovered it is much easier to fix in a digital model than in a physical production part, saving time and money by preventing the need for costly rework or retooling.
The ability to quickly create custom tooling and fixtures can also reduce production costs by allowing companies to focus on more revenue-generating work. The digital validation that comes with 3D printing allows potential errors in the CAD designs to be caught early, mitigating waste and ensuring high-quality output.
This can be especially helpful when attempting to create complex, organic-style geometry that would be difficult to make with conventional techniques. By utilizing technologies like topological optimization and generative design, it is possible to produce parts with mesh structures that are dense where stress concentrations are highest and light and airy where they are not. This can make for parts with a higher level of precision that are more resistant to failure under load.
A variety of industries are using 3D printers to produce more than just product models and prototypes, but also end-use parts and products. This includes everything from footwear to furniture, tools, wax castings for jewelry making, and even household items like bag clips and desktop organizers. Artists use 3D printers to fabricate sculptures, and archaeologists are duplicating ancient artifacts and dinosaur skeletons.
In the future, 3D printing may be able to be used for more advanced applications such as personalized medicine and tissue engineering. For example, medical researchers are experimenting with using 3D printing to produce drugs that are tailored to each patient’s unique genetic makeup, allowing for more targeted and effective treatment. Another potential application is creating prosthetics that can be designed to meet the specific needs of each individual patient. This could potentially allow for more comfortable and realistic looking prosthetics that can better mimic the function of natural limbs.
Hard Tooling
Hard tooling utilizes materials such as steel and carbide to make molds that can endure long production runs. This makes it a good option for high-volume manufacturing, especially if the project involves tight tolerances and complex geometries. It also offers excellent dimensional accuracy and surface finish. These qualities are necessary for ensuring consistent product quality across large numbers of pieces. In addition to its longevity, hard tooling reduces per-unit production costs. This is because the initial upfront costs are spread out over an extended period of time.
Soft tools offer the flexibility to adapt to different purposes. This is especially helpful for prototype development, where the production of functional prototypes is crucial to evaluating design and ergonomics as well as manufacturability. It also allows for iterative testing and reduced overall development cycles, which is essential in reducing the time to market. This makes it easier to meet production deadlines and reduce the risk of costly redesigns that may occur with traditional manufacturing methods.
The cost of 3D printing systems is significantly less than that of traditional manufacturing systems, making it a more accessible solution for a wider range of customers. It also requires much less manpower to operate and maintain. Additionally, fewer parts need to be sent away for fabrication, which reduces shipping costs and environmental impact.
Moreover, 3D printers can produce complex designs with great precision and a wide variety of material properties. This can be a boon for companies in the aerospace industry, automotive industry, and other sectors that require the creation of precision products. However, it is important to consider the specific requirements of each project before deciding on a particular type of tooling.
Parts manufacturers should take into consideration the volume of production that is required, the complexity of the design, and the time it will take to transition to a hard-tooled process. This will help them decide whether to opt for soft or hard tooling, which will help them reduce costs and bring their products to market faster. Partnering with an experienced manufacturing company can help them achieve this goal, by offering on-demand access to a cloud-connected 3D printing smart factory.
Speed to Market
3D printing speeds up the process of designing new products by reducing time spent on creating tools for production parts. It can also reduce costs by eliminating the need for expensive metal tooling. 3D printers also allow businesses to experiment with different designs without committing to expensive, large-scale manufacturing runs. This allows companies to take advantage of new business opportunities quickly and accurately.
The technology is used for a wide range of business purposes, from consumer goods to medical equipment. In addition to enhancing the quality of consumer goods, 3D printing has the potential to revolutionize health care and other industries. For example, researchers are working on using the technology to create tissue that could replace damaged organs or make prosthetics more effective.
To make a 3D-printed object, a virtual design of the desired item is first created using computer-aided design (CAD) software or another type of program that can generate precise drawings and technical illustrations. Then the model is broken down into hundreds or thousands of layers that can be printed in a single step using a technique called slicing. Each layer is created by extruding a plastic filament—usually acrylonitrile butadiene styrene, polylactic acid, or some other thermoplastic—through a heated nozzle in layers.
Depending on the material being used, the printing process can produce intricate shapes that would be impossible or prohibitively expensive with subtractive manufacturing techniques. This includes complex geometries, lattices, and internal cavities and voids. The flexibility of the technology means that customized products can be produced, such as dental and orthopedic implants or personalized consumer goods.
By moving to a rapid prototyping and mass customization approach, businesses can gain an early advantage in new markets and develop strong brand loyalty with customers. Businesses that have the fastest speed to market—especially when they deliver specific value to their target audience—are able to establish themselves in the market and attract investors and potential partnerships.
Businesses that bring production capabilities in-house with 3D printing are able to react to changing customer needs more quickly and save on shipping costs and associated tariffs. It can also help protect intellectual property and avoid costly IP theft. By printing parts closer to the end customer, they can also minimize their logistical costs and environmental impact.